Today's workplace has grown substantially since the 1800's. Among the advancements, one of the greatest improvements has come in accident prevention and safety. Previously manufacturers had an endless supply of people to fill and refill positions, people were often considered a cheap commodity.
If a man went down on the job, he would be carted off, and replaced. There were no programs to prevent accidents, and no set compensation standards to ensure that the injured worker would be compensated. There was little concern shown overall by employers for the injured workers.
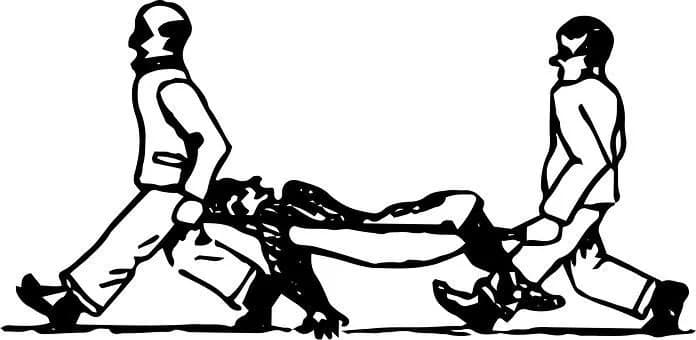
Something that triggered an increased interest in assuring worker safety and prevention were the conditions surrounding, and including World War I, and World War II. These events created severe labor shortages. All able bodied skilled persons during these times were either on the front lines, or in manufacturing factories. Both efforts supported the war. Since labor was scarce, the law of supply and demand put a greater value on the worker, and thus made protecting the interests of those workers quite significant. This management style set a precedent that has become more relevant in today's economic world, protecting your employees is a must in a competitive international environment.
Three E's Of Safety
To make a real difference on the people it was designed to protect, a proper accident prevention program started with, engineering, education and enforcement. Engineering the environment to focus on safety needs. Educating employees from the top to the bottom, and manoeuvring within the parameters of the safety rules. Lastly, the commitment from the organization to set fair rules, in a safe manner, and enforce these rules with safety at the forefront.
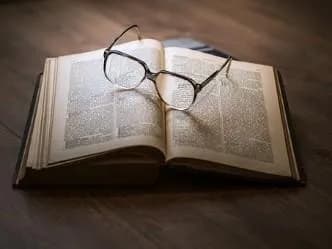
Engineering a process, product or piece of equipment to a simple, safe and less dangerous state can decrease the potential for hazards that are present in current states. Ergonomic styling, removing redundant steps, and raising loads to a manageable position are examples of small but positive engineering steps that can be made.
Education explains in the best terms to the employees, who, what, where, when, why and how the rules, and processes are to be applied. Training, assessments, and onboarding of associates must be worded to relay the legal consequences to the worker, company and customers in a manner that is intelligible and unmistakable to the audience that it is designed for.
Enforcement creates a fair check and balance system. The environment is established, and people are held accountable. All members of the organization must comply, 100% of the time. A safety team must be established, not to just enforce, but to be a constant partner for every employee. Working to create safe zones in the environments, by performing a Kaizan, or simplifying the work space with a 5-S program that lays out in no uncertain terms the design of the work space, and its intended use. With enforcement it's important to specifically note to everyone, that the team's job isn't to point fingers, but to consistently, on a daily basis create a positive work environment for all to work in safely. Rotating team members every six or 12 months is ideal for any team, by putting fresh eyes on the floor.
Results
The results from these programs are beneficial to both the employees and the company. Sending people home in the same shape they came to work in is always a great thing. The overall savings from potential compensation and medical attention, goes back into the bottom line, and benefit the employees and the company at the year-end review. A safe company is a successful company in so many ways.